Historically, manufacturing has stood out as an industry that fully uses current application autonomy. A lot has changed since the introduction of mechanical robots in the 1960s. Today's manufacturing lines must be more efficient, adaptive, and precise. In the last several years, numerous improvements to manufacturing lines have been implemented to better serve workers in their daily tasks.
Robots in the manufacturing industry are on the verge of transforming the industry as they become more intelligent, more efficient, and more cost-effective. Human-like talents and traits, such as detecting, expertise, memory, and trainability, are being put to the test by these machines. Because of this, they're up against additional jobs like choosing and packing, testing or examining objects, or putting together small devices. A new "collaborative" era of robots, on the other hand, brings a period when human professionals escort robots out of their cages and genuinely as one indivisible unit with physical displays.
Robots have been used in production for a long time to guarantee timeliness, efficacy, and productivity in these industries. However, how can a wide range of advanced robots contribute to the adaptability and flexibility needed to meet rapidly changing customer expectations and the growing need to develop new products more quickly?
Assembling and manufacturing are being transformed by robots, which are designed to move materials and perform various other tasks in production and manufacturing environments. Robots are frequently used to undertake dangerous or unsatisfying tasks for human workers, such as repetitious work that produces fatigue and might lead to injuries if the worker is careless.
Industrial robots have the potential to substantially improve product quality. Each action is carried out with precision and high reproducibility. In the workplace, robots improve productivity and safety.
The number of applications performed by robotic squads at a factory is expanding at an alarming rate. What are the chances that these robots in another plant, even one on a different continent, would be able to share information with their human counterparts? Such machine-to-machine learning sharing might make it easier for enterprises to shift production from one region to another, or from one product to another, without the enormous expenses, time, and effort required by traditional manufacturing.
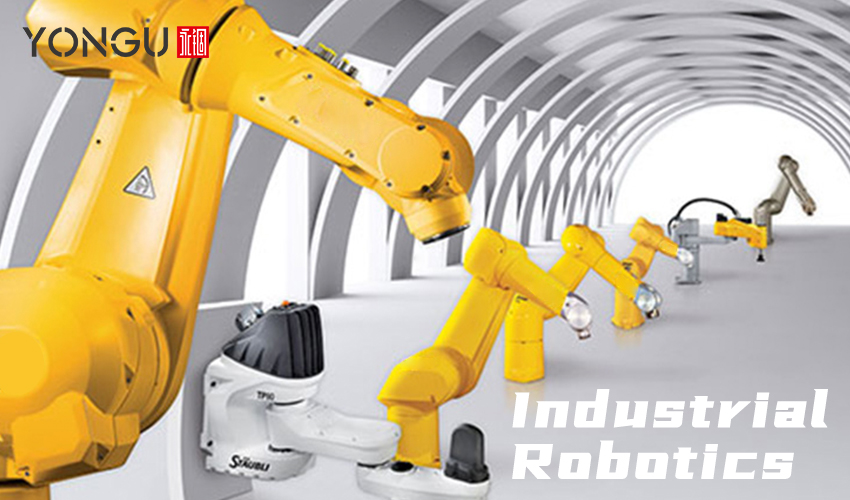
Application of Robotics in Industry
Robotics industrial applications are numerous, but some typical applications worth mentioning include the following.
Assembly & Dispensing
Manufacturing relies heavily on the assembly of discrete components into complete products. In the past, only human agility, eyesight, and intelligence could do this task. Technological advances allow robots to undertake many of these tasks. Many assembly techniques involve sealants, hence robots that distribute them are linked.
The systematic employment of robots to assemble items and eliminate time-consuming and exhausting chores has become widespread. The significant outcome of using robots technology is an increase in output and a decrease in operating expenditures.
Handling & Picking
Material handling robotics is applied in product movement, packing, and selection processes. They are also able to automate operations that are involved in the process of moving parts from one piece of equipment to another. There is a reduction in direct labor expenditures, and a significant portion of jobs formerly handled by human labor that was tiresome or hazardous are removed.Machining and Cutting
Robots can handle many monotonous tasks in a manufacturing or machine tool facility. Flexibility in robots allows us a production alternative that would otherwise be impossible to automate. Incorporating robots into your manufacturing process might make doing tasks like cutting, polishing, and grinding easier.Welding & Soldering
The robot can operate at the same pace as a man. Still, they can always keep welding and soldering, maintaining quality and quantity, boosting production, decreasing costs, enhancing workplace safety, and saving time by eliminating process parameters where a man would halt, change the component, and re-weld.
Casting & Molding
Casting is the technique of making metallic things by injecting liquid metal into a die or hollow that is curved in the form of the object that is to be manufactured. This allows the liquid metal to solidify into the desired shape of the object. Molding is quite similar to casting, with the primary difference being that plastic, though not exclusively, is utilized as the material of choice in the process. In most cases, molding is a more practical option than casting.Finishing and Sanding
Quite a few manufacturing procedures, including drilling, casting, die casting, and welding, result in unwanted material being left behind or creating ragged or sharp edges. Getting rid of this unwanted stuff is necessary to have the product finished the way it should be. Sanding and finishing are the two tasks that fall under this category that is well performed by modern robots.Cleaning & Hygiene
The cleanliness of manufacturing facilities should be maintained for the sake of the health and safety of the employees who work there and the quality of the products they produce. The act of cleaning is typically dull and repetitive since it involves a lot of the same steps. As a direct result, robots are finding more and more uses in the cleaning industry.Logistics & Storage
A logistics robot is a self-contained system or machine that automates the movement of goods, increases warehouse security, and increases output.
Robots have grown in prominence due to the widespread use of new technologies in warehouse operations, such as the reception, storage, management, processing, and shipment of items. They are responsible for various tasks, including moving goods between locations, processing orders, and storing goods on racks.
Sealing and Spraying
A sealant robot can apply glue to any sort of product since the robot has a variety of robotic arm configurations. Reliability, quickness, and consistency are the significant advantages of this application.
Inspection & Quality Control
Quality control flaws can mean the difference between life and death, such as when a part fails or is placed wrongly. In most cases, humans are just 80 percent correct. Using a robot to check a product can be 100 percent accurate.Harvesting
It is essential to harvest fruits and vegetables at the optimal time to minimize spoiling and loss of quality and to meet client demand for a product of the highest possible standard. The harvesting of grains and other crops requires a lot of effort in addition to being time-sensitive.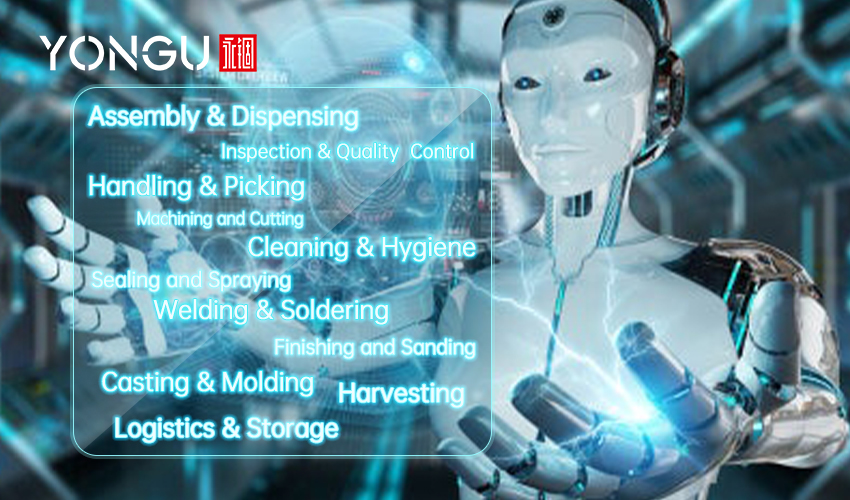
YONGU ELECTRONICS SUITED ALUMINIUM CASES
Now, the growth of the robotics industry owes a significant amount of debt to the development of aluminum beginning in the middle of the 20th century and continuing ahead. The field of robotics would not be where it is now if it were not for the qualities of strength, durability, lifespan, portability, and flexibility offered by aluminum.
In addition to being utilized in various robotic components, aluminum is essential in the automated production process. Aluminum helps supply answers in situations where other materials cannot do so, ranging from small, machined parts to massive, automatic machinery and even the robots employed to produce them.
YONGU's aluminum enclosures enable manufacturers and designers to get the most out of the goods and projects they are working on by maximizing their potential.
YONGU Cnc Milling Machine Custom Supply Motherboard Electrical Aluminum Electronic Enclosure H36 202*52mm
It has a 61 split type extrusion model (H series) to be chosen from.
Structure & Key Features
- Split type structure includes 1pc top housing, 1pc bottom housing, 1pc front panel, and rear panel.
- Good heat dissipation, easy to be assembled.
- L shape brackets for panels can be customized to wall mount.
- Dimensions, hole drilling, surface treatment, printing, etc., can be customized.
- Rugged and robust for heavy-duty use.
- Durable and can be used for a long time.
- Good quality aluminum material, al6063, and al5052.
- It can be used for din rail.
For further information and customized product of your requirements, please follow our FACEBOOK for more updates and informations: https://www.facebook.com/Foshan-Gof-Electronic-Machine-Co-Ltd-104706631749290
You can also contact us at +86 13326782625 or write us [email protected].