PLC Working
Data is provided into the programmable logic controller, which evaluates it and then generates essential outputs based on the parameters of the program being fed into it. Based on inputs and outputs, a PLC can easily track and maintain a runtime log of temperatures, production yield, trigger alerts, and more. PLCs are adaptable to industrial process control systems that may be employed in various contexts.
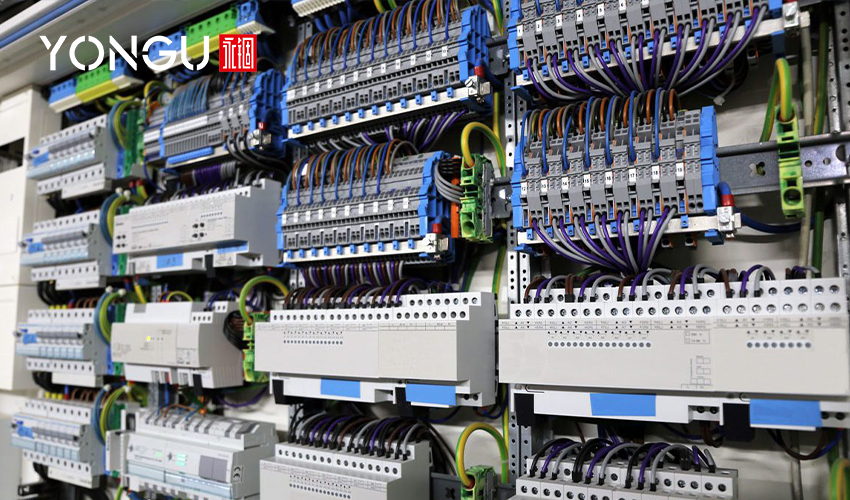
PLC Hardware
PLC hardware consist of the following:
Central Processing Unit (CPU)
The CPU module consists of a core processor, ROM memory, and RAM. ROM contains an OS, peripherals, and applications. RAM stores data and applications. PLCs have octal or hexagonal CPUs. This CPU replaces timers, relays, and counters. CPU receives sensor data, analyzes it, and delivers control commands.
Memory
While random access memory (RAM) holds information about input and output devices, timers, registers, and other internal devices, system ROM stores data that is fixed permanently and is needed by the CPU.
I/O Module
An input & output module is an unique module for connecting inputs and outputs in a PLC.
Input device transmits and control data signals to a processor. They may include sensing devices, limit switches, and proximity sensors etc.
Output devices are any devices used to transmit data processing results and transfer the information into an understandable form. They may include motors, pumps, fans, etc.
A microprocessor can effectively communicate with input and output devices with the assistance of an I/O module.
Communication Interface Module
Using adaptive I/O modules, data is conveyed between CPUs and communication networks. Remote PLCs and PCs can be linked with the aid of these communication modules.
Power Supply
To power the entire PLC system, this module is needed. It envloves the mechanism of converting AC power into DC power and then stepping down to requird voltage. A 24V DC source powers the majority of PLCs. Isolated power supplies are uncommon in PLCs.
Types of PLCs
Compact and modular PLC are the two types of programmable logic controllers.
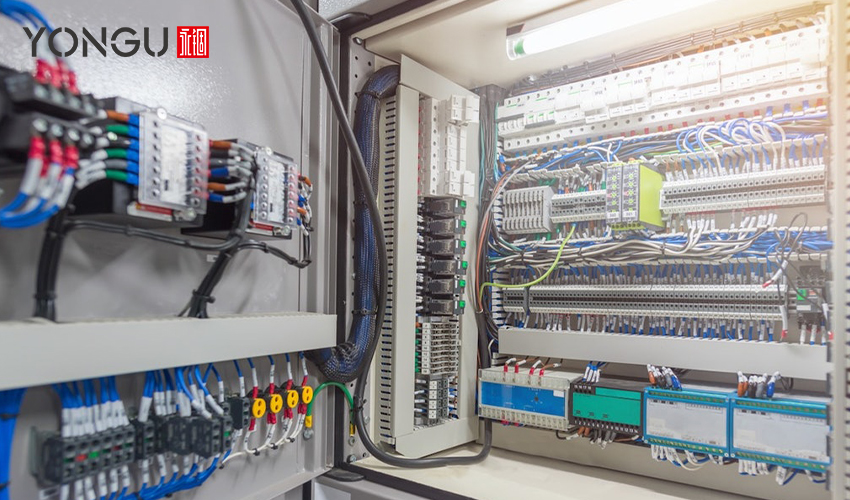
Compact PLC
Many different modules would be included within a single enclosure. It comes with a predetermined quantity of I/O modules and additional I/O cards. Therefore, it has no optional capacity to expand the modules. The manufacturer would have complete control over both the inputs and the outputs.Modular PLC
It refers to the type of PLC that allows for different expansions to be implemented using "modules." It is possible to add more I/O components. Because one component may function independently from the others, it is much simpler to utilize.PLCs in Robotics
When the Programmable Logic Controller (PLC) first emerged, it symbolized the beginning of a new era in production. More and better-quality items were produced at a lower cost due to factory floor processes being more automated, more accurate, and less expensive. Modern technology has transformed how PLCs are employed in different sectors.
PLCs are the brains of industrial robots, dictating how and when they do their work. Like a philharmonic orchestra conductor, a PLC orchestrates a "symphony" of robots. They all work together toward a shared objective or product or complete the process by following the instructions of the PLC.
PLCs are elegant pieces of art in their selves. When it comes to protecting them from heat, humidity, and vibration in the industrial environment, YONGU aluminum alloys play a critical role because of their low density, high strength-to-weight ratio, superior corrosion resistance, and comparatively cheap rates compared to composites.
Traditional robotic applications link a machine to an external PLC. As more factories and warehouses use robotic in their operations, they must decide how to govern it. OEMs supply their own tightly integrated controller; however, newer advances permit PLC control. Integrating robotic control inside a PLC may be preferable to using an OEM proprietary controller in facilities that currently utilize PLCs for other machine controls.
A PLC-based robot system does not need training in a specialized OEM operating language because most engineers and technicians are already familiar with PLCs. To operate, maintain, and manage robotic systems, operators still have to comprehend how robots work, but using existing PLC expertise dramatically decreases training time. The following common features of PLCs make them even more efficient:
- Programming Controls
- Software Interfaces
- Program backup
- Program Documentation
System integration of robots and non-robotic components is common regarding robotic material handling. For intended functionality, robotic controllers must interface with the control algorithm, interprocess communication data, and safety mechanisms since PLCs often control non-robotic system components. Interfacing various control modules in a complicated application might be a challenge.
Because the link between different control systems is eliminated, the system complexity is considerably reduced when a single PLC controls robots and other related components. OEMs and end-users benefit from reduced integration and development expenses when different processes and equipment are handled by a single controller, which could increase revenue in the long run.
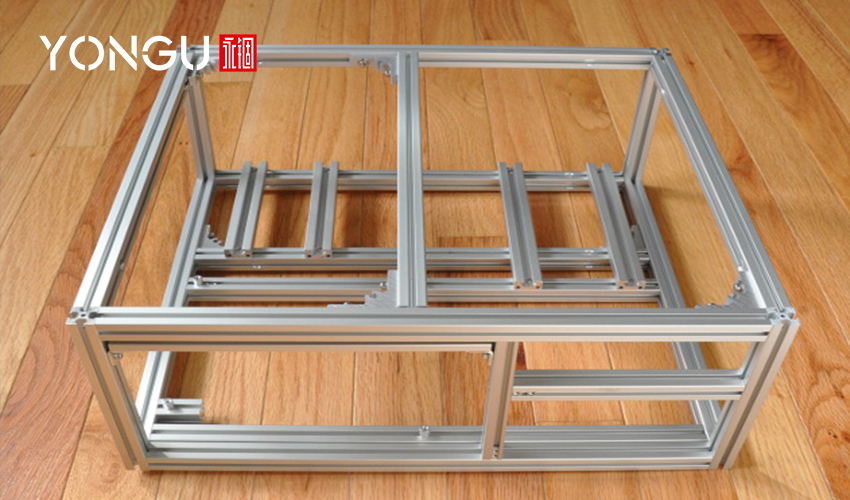
Shared Control Architecture
With PLC-based robotic controllers, conventional automated equipment and robots may be controlled from the same interface as other facility machinery. Drawing nomenclature such as wire numbering should be consistent with other devices in the same control panel when designing a robot controller. The following are additional advantages of a unified control architecture:
- Maintenance and diagnostics are now much easier to do.
- significantly smaller panel's overall footprint.
- Streamlined instruction.
- Common spare parts.
- Standard method for assigning component numbers.
Most proprietary OEM controller I/O communications include integrating with a PLC. PLC-based robotic controls avoid this unnecessary communication but connect with the robot's I/O, a straightforward procedure. PLC-based robotic controls simplify I/O communication and let operators utilize PLC hardware, I/Os, and communications protocols instead of OEM controllers.
Common Interface
Rather than using a teach pendant to communicate with the robot controller, a PLC-based robotic control system provides a standardized human-machine interface. Now, all of the HMI's capabilities, such as alarms, malfunction recording, real-time tracking, etc., may directly communicate with the robot's control system. Individual errors and individualized procedures can be added to or altered directly through the robot controller. There is less operator training required for the HMI interface since it is more application-specific and has a more flexible structure.
Reduced Maintenance and Upgradation Cost
Admixtures, crackers, palletizers, wrappers, and conveyors are often controlled by PLCs in manufacturing facilities, which incorporate several types of machinery. Maintaining and upgrading an integrated system might be a headache if each OEM provides its control scheme. As a result, most requests for proposals for manufacturing facilities restrict the controllers and hardware that OEMs may employ.
The total cost of ownership can be reduced by using a single control system that simplifies updates and maintenance. In this regard, using a PLC-based control system in robotics results in cheaper ownership costs by saving end-users the expense of a distinct robotic control design.
Compatibility Enhancement
Numerous industrial robot operations opt to stick with their present brand given the complex nature of OEM robot interfaces and the requirement for training. Companies are frequently hesitant to support various robot brands or connect different OEM controllers, preventing them from picking the best-fit robot model. End customers are no longer "locked in" when choosing subsequent solutions due to PLC-based robotic controllers.
PLC-based robotic controllers provide integrators with additional options. Due to a considerable customer base and particular application needs, it is improbable that robot-intensive settings, such as the automobile sector, would transition from using OEM controllers. Certain robot OEMs do not provide a provisioning method for a PLC-based controller.
When deciding on a robotic controller, the operations department needs to consider each option's cost, availability, and functionality.
YONGU ELECTRONICS SUITED ALUMINIUM CASES
Now, the growth of the robotics industry owes a significant amount of debt to the development of aluminum beginning in the middle of the 20th century and continuing ahead. The field of robotics would not be where it is now if it were not for the qualities of strength, durability, lifespan, portability, and flexibility offered by aluminum.
In addition to being utilized in various robotic components, aluminum is essential in automated production. Aluminum helps supply answers in situations where other materials cannot do so, ranging from small, machined parts to massive, automatic machinery and even the robots employed to produce them.
YONGU's aluminum enclosures enable manufacturers and designers to get the most out of the goods and projects they are working on by maximizing their potential.
YONGU Eletrical Plastic Cover Box K21C 160*55mm
It has 23 models to choose from, including the following specifications.
- K01A-K05A, full plastic protected plastic covers.
- K01B-K05B, half-protected plastic covers with aluminum end panels.
- K06-K10, half-protected plastic end covers.
- K11-K23, wall mounted flange and can use the sticker instead of the printing.
Structure & Key Features
- Good heat dissipation, easy to be assembled.
- Dimensions, hole drilling, surface treatment, printing, etc., can be customized.
- Rugged and robust for heavy-duty use.
- Dustproof, Durable and can be used for a long time.
- Good quality aluminum material, al6063, and al5052.
- Conductivity is achievable using contacts between unfinished inner surfaces.
For further information and customized product of your requirements, please follow our FACEBOOK for more updates and informations: https://www.facebook.com/Foshan-Gof-Electronic-Machine-Co-Ltd-104706631749290
You can also contact us at +86 13326782625 or write us [email protected].