1.Product Quality: The presence of contaminants in a material or substance can significantly impact product quality.
2.Process Efficiency: Powder or tiny particles in a substance might reduce throughput.
3.Compliance with Regulations: A wide variety of businesses must comply with regulations that demand that they identify and manage the presence of pollutants or other foreign particles in their products. Manufacturers must comply with these rules to guarantee that goods are risk-free and up to par with quality standards.
4.Controlling Expenditures: Identifying the presence of powder or tiny particles in a substance can aid in the avoidance of waste and the saving of money.
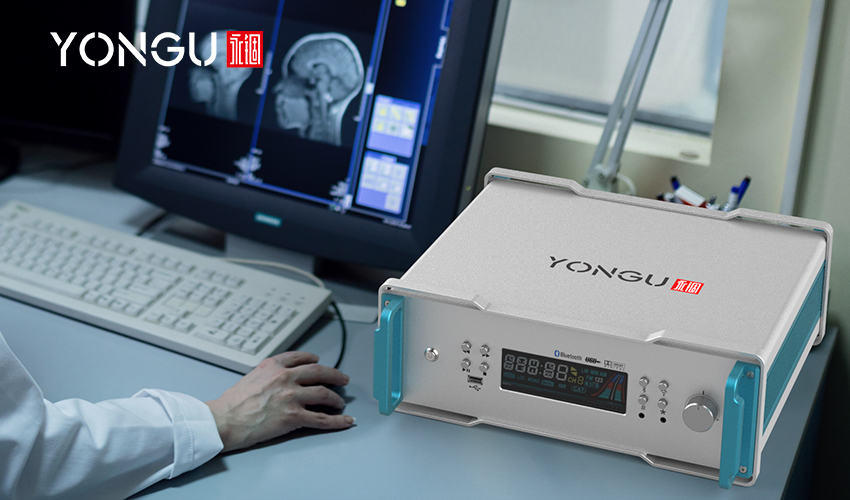
WHAT IS POWDER DETECTION EQUIPMENT?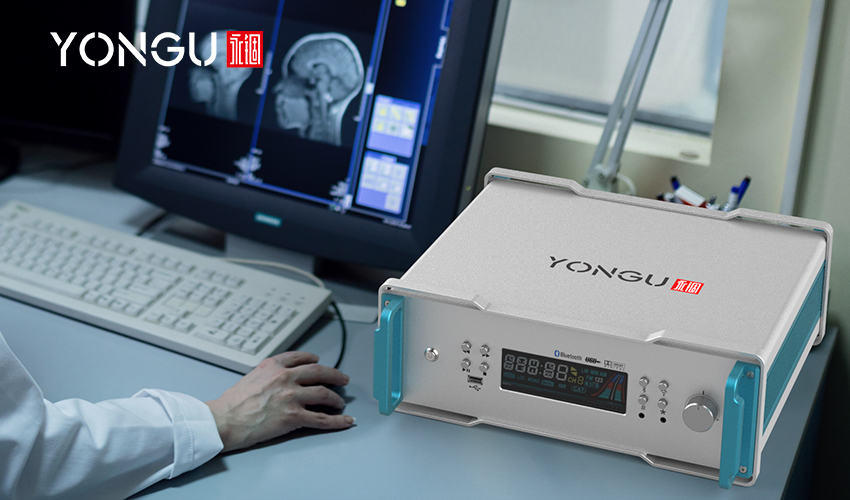
Powder detection equipment is any gear or technology that can identify the presence of powder or small particles in a given material or substance. These machines see widespread use in the pharmaceutical, food, and chemical industries, among others, for producing and processing powders.
Equipment that detects powder may employ various techniques, including those based on light, electricity, sound, or x-rays. Because of these techniques, machinery can detect powder particles even when present in minute numbers or inaccessible locations.
Powder detection equipment is crucial for avoiding product contamination and wastage and maintaining product quality. As a result, manufacturing processes can be made more efficient and accurate, with less time spent on inspection and a higher output rate.
TYPES OF POWDER DETECTION EQUIPMENT
Here is a quick rundown of the essential components and structures of the many types of powder detection equipment and their respective industrial applications:
1.Optical Sensors: Optical sensors can detect powder particles, which employ a light source and a receiver. A beam of light is emitted from the light source and transmitted through the substance under examination; the receiver then detects variations in the light caused by the presence of particles. Optical sensors can be installed in various settings, including on conveyor belts and in other processing machinery, as either single- or multi-point detectors.
To ensure the safety of their products, the pharmaceutical and food industries frequently employ optical sensors for this purpose. Capsules, tablets, and powders are commonly inspected using these devices because they are sensitive to even the tiniest contaminants.
2. Electromagnetic Sensors: The presence of powder particles can be detected by electromagnetic sensors utilizing a magnetic field. The sensor comprises a coil that emits an electromagnetic field and a receiver that picks up on fluctuations in that field due to the presence of particles. These sensors can be customized to identify the presence of metals and other conductive elements within a substance.
The chemical and food sectors frequently turn to electromagnetic sensors when looking for metal contamination in powders or liquids. Often employed in combination with other sensors, they can identify a wide variety of metals, both ferrous and non-ferrous.
The chemical and food sectors frequently turn to electromagnetic sensors when looking for metal contamination in powders or liquids. Often employed in combination with other sensors, they can identify a wide variety of metals, both ferrous and non-ferrous.
3.Acoustic Sensors: Acoustic sensors use resonating airborne sound waves to detect the presence of powder particles. The particle sensor works via a transmitter that sends sound waves and a receiver that picks up on wave variations triggered by particles' presence. Powder flow or particle size variations can be detected with these sensors.
Powder flow and particle size variations are easily detected using acoustic sensors used often in the pharmaceutical business. They are sensitive enough to pick up on variations in powder's acoustic signature due to flow rate, density, or particle size changes.4. X-ray Fluorescence: The presence of metals and other substances can be detected using an X-ray fluorescence detector. The detector fires a beam of X-rays through the sample and then measures the X-rays' absorbed energy. This can be used to detect the existence of individual elements.
Metal contamination in ores, minerals, and concentrates can be detected with the help of X-ray fluorescence detectors, which are widely employed in the mining and mineral processing sectors. They're used to check on the purity of ore and concentrate and are sensitive enough to identify a wide variety of metals, even trace ones.
In summary, detecting impurities or other particles in a substance relies heavily on the quality of the equipment; thus, its construction and design are crucial. Several sectors benefit from the usage of powder detection instruments of varying types. Having these instruments on hand during the production and processing of powders is essential for maintaining a high-quality standard, avoiding contamination, and maximizing productivity.
WHY ARE ENCLOSURES NECESSARY FOR POWDER DETECTION EQUIPMENT?
Powder detection equipment can be shielded from environmental elements that could compromise its performance or accuracy by placing it inside an enclosure. Powder detection devices benefit significantly from enclosures for the following reasons:
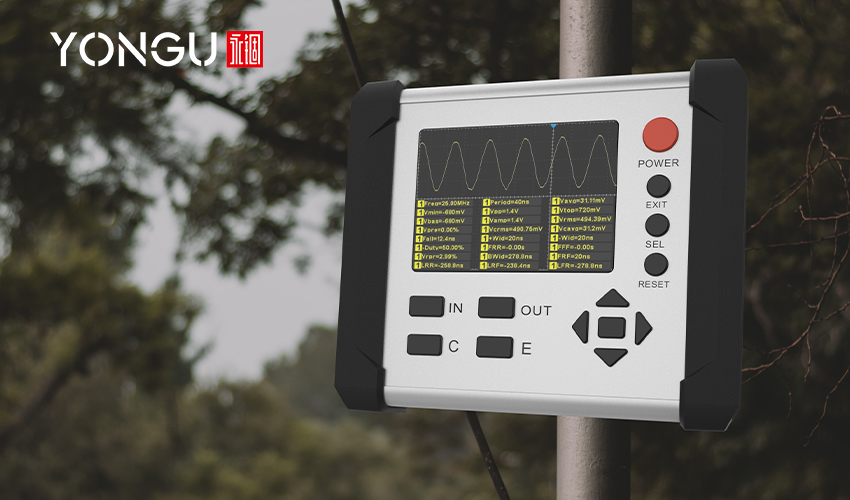
YONGU ENCLOSURE SERIES FOR POWDER DETECTION EQUIPMENT
Depending on the unique needs of your application, YONGU provides a selection of box enclosures that could be appropriate for powder detection equipment. These enclosures can be found here and can be customised as per customer needs. While choosing an enclosure from YONGU, consider these general instrument enclosures as you browse our selection.
A Series
A series of enclosures have 12 models and include the following features:
G series enclosures have 17 models and include the following features:
For further information and customized product of your requirements, please follow our FACEBOOK for more updates and informations.
You can also contact us at +86 13326782625 or write us [email protected].
Metal contamination in ores, minerals, and concentrates can be detected with the help of X-ray fluorescence detectors, which are widely employed in the mining and mineral processing sectors. They're used to check on the purity of ore and concentrate and are sensitive enough to identify a wide variety of metals, even trace ones.
5.Nuclear Magnetic Resonance: In nuclear magnetic resonance, powder particles are located with magnetic fields. The detector comprises a coil that produces a magnetic field and a receiver that detects fluctuations in the field induced by the presence of particles. These detectors can identify specific chemical compositions or crystalline formations.
The pharmaceutical sector frequently employs nuclear magnetic resonance detectors to identify the presence of particular chemical structures or crystal formations in powders. A powder's chemical makeup, purity, and crystalline structure can all be determined with their help.In summary, detecting impurities or other particles in a substance relies heavily on the quality of the equipment; thus, its construction and design are crucial. Several sectors benefit from the usage of powder detection instruments of varying types. Having these instruments on hand during the production and processing of powders is essential for maintaining a high-quality standard, avoiding contamination, and maximizing productivity.
WHY ARE ENCLOSURES NECESSARY FOR POWDER DETECTION EQUIPMENT?
Powder detection equipment can be shielded from environmental elements that could compromise its performance or accuracy by placing it inside an enclosure. Powder detection devices benefit significantly from enclosures for the following reasons:
1.Enclosures keep the dust and debris out, which could clog the sensors or skew the findings from powder detection equipment. The machinery can keep working as intended by keeping them out of the enclosure.
2.Moisture and rusting can damage the sensors and other parts of powder detection equipment, but enclosures keep them safe from the elements. There is also the possibility of readings being distorted by moisture.
3.Enclosures are essential to any industrial workplace, Protecting workers from potentially harmful substances and tools. By enclosing the machinery, operators can prevent themselves from coming into contact with harmful elements.
4.A wide variety of commercial sectors are subject to rules that demand that they safeguard their machinery from environmental conditions that have the potential to impact how well they function. It is vital to comply with these regulations to guarantee that the equipment will give accurate and dependable results.
In conclusion, enclosures are crucial for powder detection equipment as they prevent damage from the elements, safeguard operators and aid businesses in meeting regulatory requirements.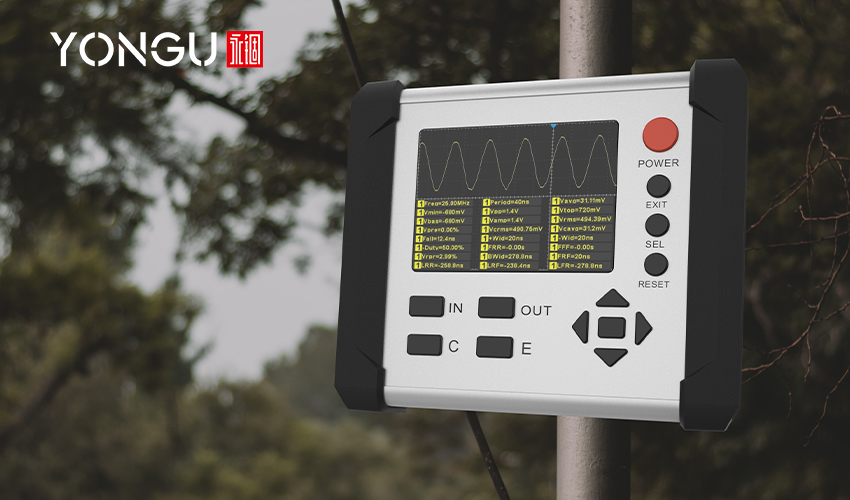
YONGU ENCLOSURE SERIES FOR POWDER DETECTION EQUIPMENT
Depending on the unique needs of your application, YONGU provides a selection of box enclosures that could be appropriate for powder detection equipment. These enclosures can be found here and can be customised as per customer needs. While choosing an enclosure from YONGU, consider these general instrument enclosures as you browse our selection.
A Series
A series of enclosures have 12 models and include the following features:
- Thickened Panels
- Strong Load Bearing Capacity
- Strengthened Enclosure Structure with Aluminum Alloy Corners
- Modular Side Panels for easy installation
- Heat dissipation design
- Anodizing colours for the whole set can be customized
- Customized length, width and height
G series enclosures have 17 models and include the following features:
- Custom aluminum enclosures, G01-G06, height is settled, and width and length can be changed.
- G12-G17, rack mount case. 2U/3U/ can be chosen.
- Customized hole drilling, surface treatment and printing
- The rack is mounted and can be placed on the table.
For further information and customized product of your requirements, please follow our FACEBOOK for more updates and informations.
You can also contact us at +86 13326782625 or write us [email protected].