TYPES OF TEMPERATURE MONITORING
Different applications and settings call for different temperature monitoring techniques. Standard methods of measuring temperatures include:
1.Contact Temperature Measurement
Through this technique, a probe or thermocouple makes physical contact with the substance under investigation. A thermometer or data logger at the other end of the probe or thermocouple reads the temperature and stores it.
2.Non-Contact Temperature Measurement
This non-contact technique utilizes infrared technology to determine the temperature of a target. The heat emitted by an item can be measured with an infrared thermometer or captured with a thermal imaging camera.
3.Data Loggers
These gadgets are electronic thermometers that can take readings at set intervals. These can record temperature readings over time, allowing for retrospective analysis.
4.Wireless Temperature Sensors
These sensors report temperatures to a central control system through wireless technology. Used in places where wiring would be impractical, such as out in the middle of nowhere or a tight space.
5.Thermal Imaging
A thermal imaging camera takes a picture of the object or area under observation. Then the picture is analyzed to find out how the temperature is distributed. Whether you need to locate hotspots in machinery or track down a hotspot across a vast area, this technique will do the trick.There are benefits and drawbacks to using various methods to monitor the temperature. The accuracy and precision needed in a given application will determine the method used.
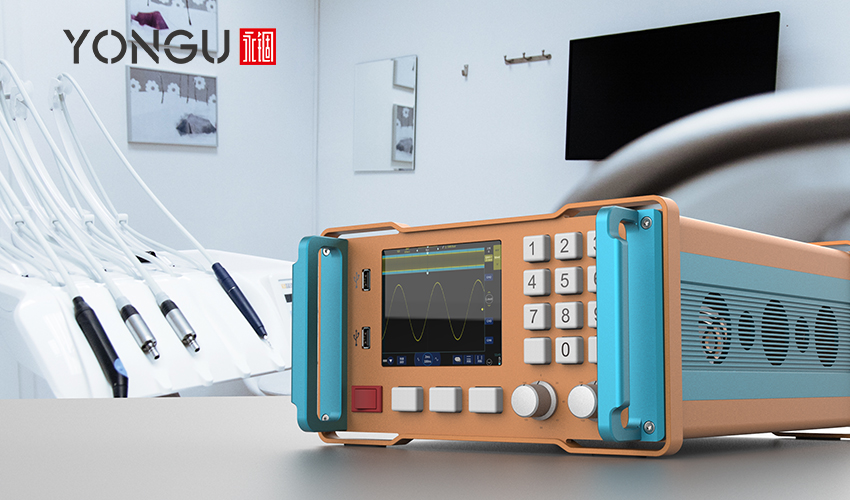
BENEFITS OF TEMPERATURE MONITORING IN INDUSTRIAL SETTINGS
Monitoring the temperature of various machinery, pieces of equipment, and rooms is an integral part of any industrial setup. This method is essential for sustaining a safe working environment, maximizing output, and protecting expensive machinery from wear and tear.
Here, we'll look at why businesses need to monitor temperatures.
1.Improved Equipment Performance and Efficiency
Equipment and machinery function best when kept in an ideal environment, and temperature monitoring is vital. Technicians can prevent performance issues before they occur by monitoring the temperature to see if it strays outside the acceptable range. Overheating and underheating can both significant harm machinery, necessitating costly repairs.Also, energy use and expenditures can be minimized by keeping equipment at its optimum temperature.
2.Reduce the Risk of Downtime and Equipment Failure
Businesses may incur significant losses due to equipment breakdowns and subsequent downtime. Production delays, decreased output, and higher maintenance expenses are all possible outcomes of machine breakdowns. The monitoring of temperatures can assist in avoiding costly equipment failure by revealing any temperature fluctuations that may suggest a problem. By catching problems early, technicians have a better chance of averting a catastrophic failure and cutting down on downtime.
3.Better Quality Products
It is essential to monitor temperatures in the pharmaceutical, food, beverage, and chemical manufacturing industries to ensure the highest quality of finished goods. These sectors must operate within strictly regulated temperature limits to maintain product quality and safety. There is a correlation between temperature and product degradation, contamination, and shorter shelf life.In these fields, constant temperature monitoring is essential for preserving product quality and safety during storage and transport.
4.Regulatory Compliance
For safety and legal reasons, temperature monitoring is crucial. The pharmaceutical, medical device, and food/beverage industries, among others, are subject to stringent temperature control standards. Losing one's business license or facing criminal charges for violating these rules is possible.Putting in place temperature monitoring systems helps firms verify they are in full compliance with all applicable regulations.
5.Improved Safety
Extreme heat in the workplace can endanger workers in several ways. Heat-related ailments, such as heat exhaustion and heat stroke, can be avoided with proper temperature monitoring in the workplace. Overheating machinery is another potential threat that can be spotted by monitoring temperatures and corrected by specialists before a fire eruption.Ultimately, it's clear that keeping an eye on the temperature is essential in manufacturing facilities and industrial settings. It's crucial for meeting regulatory requirements, producing high-quality goods, keeping workers safe, and maximizing productivity from your equipment. Organizations can save money, time, and energy by installing temperature monitoring systems and reaping the resulting gains in efficiency and output.
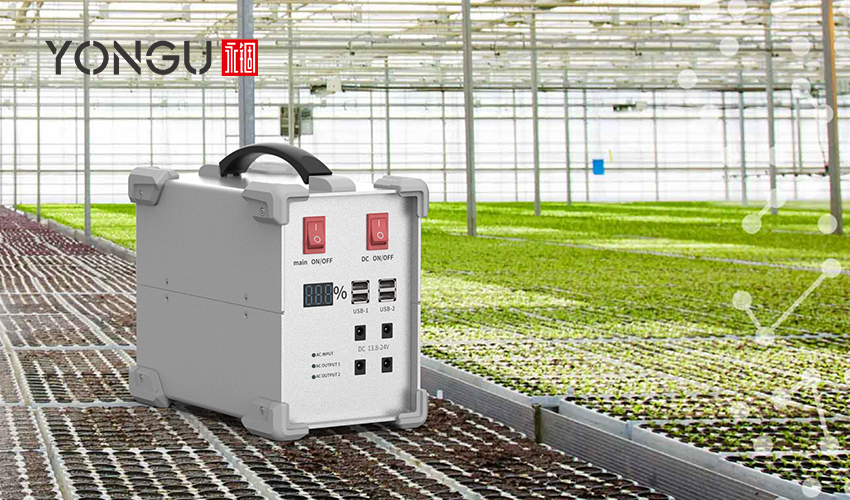
ENCLOSURES FOR TEMPERATURE MONITORING EQUIPMENT
Protection against moisture, dust, and temperature extremes is essential for monitoring devices, including probes, data loggers, and wireless sensors. They need to be enclosed for safety and optimal performance. Standard enclosures for temperature monitoring devices include:
1.Explosion Proof Enclosures
Explosion-proof housing is constructed to withstand the destructive force of explosive gases or vapors in a potentially dangerous environment. Therefore, they are constructed so no stray sparks or arcs can ignite the combustibles.
2.Heat Resistant Enclosures
A heat-resistant enclosure is a protective case for temperature sensors. They find widespread use in environments with high temperatures and wide swings in temperature.
3.Portable Enclosures
Protect your temperature monitoring equipment on the go with a portable enclosure. They are constructed from sturdy materials like plastic or metal and often feature carrying handles or straps.The type of equipment, the intended usage environment, and any regulatory requirements all play a role in determining the best enclosure for temperature monitoring devices. To ensure you get a suitable enclosure, it's best to talk to an expert about it.
YONGU INSTRUMENT ENCLOSURES
A Series
It is available in 61 different models with the following unique features:
- Strong load-bearing capacity
- Aluminum alloy-protected corners
- Strengthen structure
- Modular side panels for easy installation.
- Customized options for Dimensions, hole drilling, surface treatment, and printing
- Aluminum CNC Machining Case
- The side plates are equipped with heat dissipation effects
- The rubber feet pads are slip-proof and moisture-proof and have a protective effect on internal components.
It is available in 9 different models with the following unique features:
- Instrument Enclosures
- Customizable dimensions, cut out, colours and printing
- Thickened panel
- Precision processing with customization options.
- Strong load-bearing capacity
- Aluminum alloy-protected corners
- Strengthen and crashworthy structure
- Modular side panels for easy installation
Its unique features include:
- NEMA and IP rated Enclosures
- Concise lines in appearance design.
- Increase sense of agility.
- Expressing science and technology.
- Customized dimensions, hole drilling, surface treatment, and printing.
- The design refers to the arch bridge.
- are 6mm Panels thickness, which means nuts can be used to settle the display on the backside.
- Handles can help hide the screws expose on the surface.
You can also contact us at +86 13326782625 or write us [email protected].