How does it work? The mechanical engine transfers mechanical power from the engines to the central oil pump, which provides water pressure for the controller systems of the primary and secondary flight controls, landing gear operation, retraction, and braking, among many other systems requiring motors. This is done using a system of pipes running throughout the entire aircraft.
Air Craft Primary Control Surfaces
There are three main aircraft primary control surfaces which we are going to discuss below.Ailerons
There is one aileron on each side, and they are located at the back edge of the wings. When they move, they move in opposite to one another. As one increases, the other falls. They reduce the lift on the other wing while raising it on one. The role that allows the aeroplane to turn is made possible by that motion.
Elevator
The elevator is mainly placed near the back of the aircraft. It manages pitch, helping the face to point upward or downward. Since airplanes are often nose-heavy, the elevator forces the back of the plane downward to balance it out. The elevator, a crucial component of the motion control system for the aircraft, is also what causes the aircraft to rise or lower.Rudder
The rudder controls the rotation of an airplane. The way it moves the aircraft right, or left is just like a container ship rudder. The negative rotation drag, on the other hand, is what it is mostly used to resist. Ailerons lower, which causes it to happen.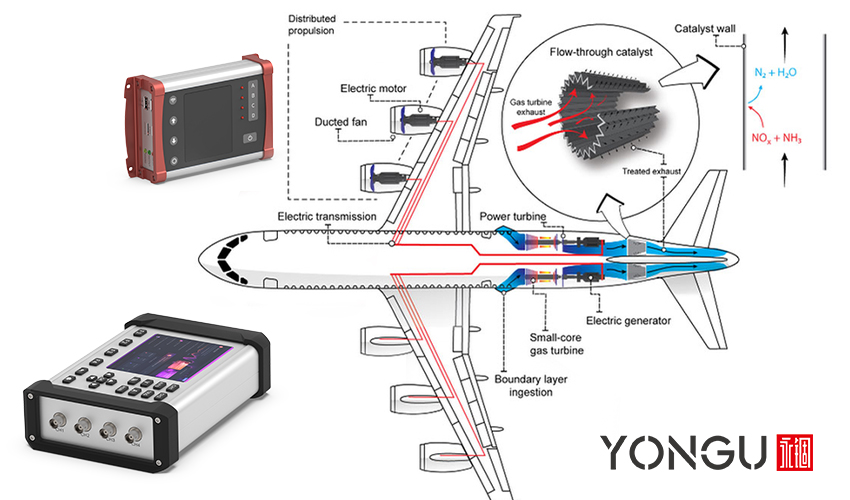
Aircraft Throttle Control
The control design issue is to change operating points while remaining within the safe operational limits, represented by the maximum and minimum fuel flow restrictions with aircraft throttle control and the mechanical limitations of the different engine components.The maximum flow limit stops the engine from overheating, and the minimum flow limit prevents the engine from starting. Wave prevention and leading shaft rotating speed are two additional operational safety limitations that are significant.
To guarantee safe and dependable operations over the flight envelope, this Article will discuss the fundamental concepts underlying modeling the motor system for control system design and how numerous safety and operational constraints are applied in engine control.
Flight Simulator
The difficulty of larger aircraft, the cost of operating them, and the test of the aircraft throttle control system they operate in are the three drivers that drive the rising usage of flight simulators in training. The size, design, and equipment of today's simulators perfectly mimic those of an aircraft's cockpit.With the help of the 3 motion platform they are mounted on, they replicate the surrounding environment and give the user a genuine perspective of flight. The ability to educate pilots in emergencies using flight simulators may be the most important use of these tools since it allows crews to safely practice scenarios that would be unsafe to practice during actual flight training.
For normal proficiency and transition training, however, the computer is much more costly than operating actual aircraft. Simulator training is sufficiently accurate that airline crews will occasionally become certified on an airplane in a simulator before ever flying the real aircraft.
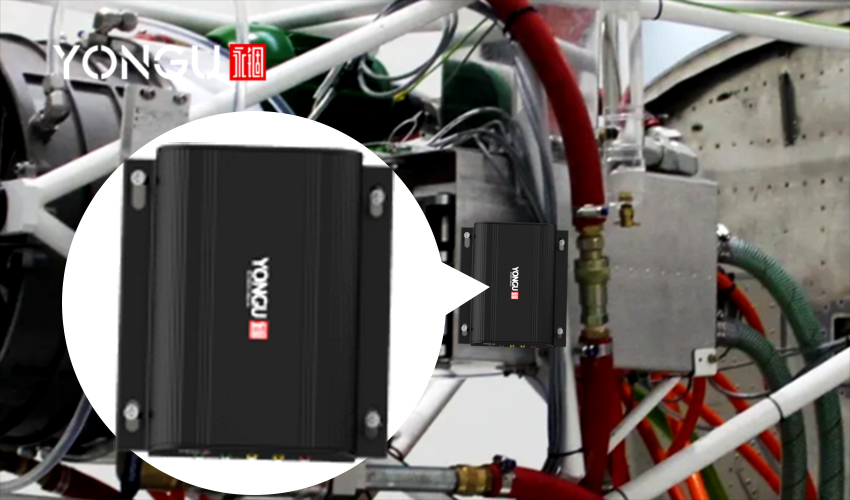
Types of aircraft
A variety of methods exist for classifying aircraft. The difference between objects that are massless and objects that are denser than air is the main one.Lighter than Air
When loaded with a gas less than air (warmed air, gas, or helium), an aircraft like a balloon, nonrigid airship (blimp), or dirigible displaces the surrounding atmospheric air and floats, much like a cork does on the ocean.As they drift with the wind, balloons cannot be steered. Deformable airships, which have experienced a resurgence in popularity and use, lack a rigid construction and have a specific aerodynamic shape that includes cells loaded with the hoisting agent.
They can be operated in all three flight axes and have a propulsion supply. Dirigibles, a type of lighter-than-air craft with a stiff interior construction that was often very big and was able to fast speeds, are no longer in use.
The majority of these dirigibles met with failure, either by exploding in a storm, as happened to the American craft Akron, Shenandoah, and Macon, or by hydrogen ignition, as happened to the German Hindenburg in 1937. It proved impossible to build dirigibles strong enough to endure the routine operation in all weather conditions.
Heavier than Air
This aircraft throttle control requires a power supply to deliver the thrust needed to achieve lift. Kites are an easy heavier-than-air craft. These typically consist of a flat-surfaced construction with a stabilizing tail connected to a rope fixed to the ground by a harness.The response of the wire material to the wind produces lift. Autonomous aerial vehicle (UAV), sometimes known as drones or occasionally remotely piloted vehicles, is another type of aircraft (RPVs).
These aircraft are employed for military and scientific objectives and are microphones from the air or the ground. Heavier-than-air (HTV) vehicles must be deployed to gain lift. These consist of sailplanes, gliders, and hang gliders.
YONGU Enclosures for Aircraft Equipements
YONGU is the best production company for electronic enclosures. Materials that are used to make them are aluminum, steel, stainless steel, copper, and plastic. available in installation styles for the panel and motor. Enclosures are used for services such as protection against sprinkling water or oil, dropping dirt, rain, rain, snow, ice, air dust, and other environmental components. Size, doors, hinge types, viewing glass, powder coating finishes, knockouts, and material are among the many customizations.These can be used by any facility that runs a lot of electric motors, including the automotive sector and various commercial installations. We at Yongu Box provide the L-series enclosures that safeguard Motor control center hardware.
IP68 waterproof casing from the YONGU L series, custom-designed for the box. B, C, and D are four distinct models that come in full aluminum (model A) and half aluminum in boxes with plastic coverings (models B, C, and D). The width, length, and height may all be modified, and there are ten various dimensions available.
Conclusion
In the end we hope you understand how does Aircraft motor control work. All pro power is produced by an aircraft's motor. Air is pulled from the high-pressure compressor of the engines to power the environmental control system and supply warm air for the aerofoil ice protection system. By understanding how aircraft motors work, we can help make sure that the systems that control these motors are reliable and safe. At Yongu, our team of experts understands how to build enclosures that protect aircraft motors from the environment and ensure their long-term reliability. If you need assistance with designing an enclosure for your aircraft motor system, don’t hesitate to reach out to us. We would be happy to discuss your needs and provide a custom solution that meets your requirements.For further information and customized product of your requirements, please follow our FACEBOOK for more updates and informations.
You can also contact us at +86 13326782625 or write us [email protected].