Aluminium is a robust, nonmagnetic, cost-effective, and corrosion-resistant material.
Here is what you need to know about the most popular aluminium alloys used in CNC machining and how to choose the best one.
TYPES OF ALUMINIUM FOR CNC MACHINING WITH PROS & CONS
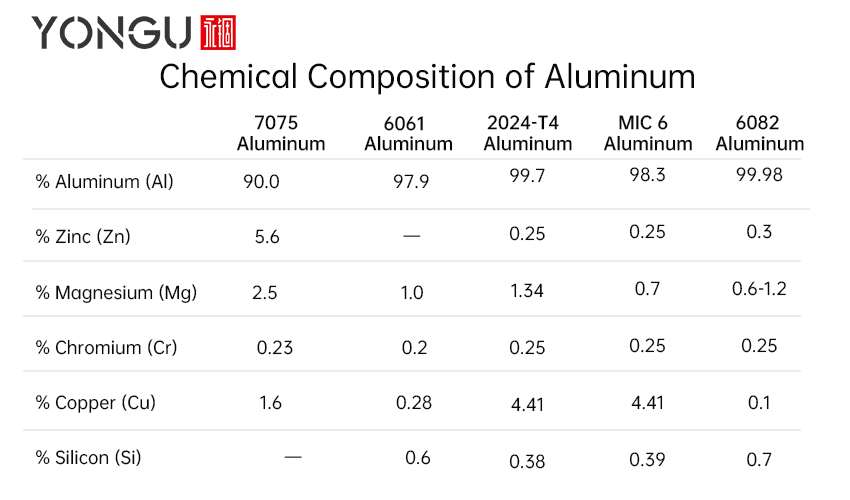
Aluminium 6061-T6
A popular aluminium alloy, 6061-T6, is commonly used in CNC machining since it is widely available commercially. In addition to being multifunctional and easy to process, 6061 may also be subjected to various thermal treatments.
6061-T6 is a great material for a wide range of applications. Despite its excellent strength-to-weight ratio, this material is unsuitable for use in high-stress environments. Automotive parts, including axles, bicycle frameworks, actuators, computer peripherals, and much more, are all common uses. The material's ultimate tensile strength is 310 MPa, and the elongation percentage before breaking is 17%. The hardness of the material is measured at 60 HRB, while the modulus of elasticity is 68.9 GPa.
Aluminium 7075-T6
When designing for highly stressed environments, engineers should think to consider 7075-T6. The exceptional strength-to-weight ratio of this particular grade of aluminium is well-known. Its durability can even resemble some steels with a smoother grain structure.
Fuse parts, missile parts, and other high-stress components are among the most typical uses in the aerospace industry. Details composed of aluminium 7075-T6 can be found on several high-end bicycles and athletic items.
Although 7075-T6 has good mechanical qualities and high strength, it also has some downsides. This material's flexibility and corrosion resistance are lower than those of other grades. A further disadvantage of aluminium 7075-T6 is its high cost, which may be impractical for some business units. The material's ultimate tensile strength is 434 to 580 MPa, and the elongation percentage before breaking is 10 to 15%. The hardness of the material is measured at 79 to 86 HRB, while the modulus of elasticity is 69 to 76 GPa.
Aluminium 2024-T4
An alloy of moderate to high strength, aluminium 2024-T4 has good ductility and tensile properties. Compared to 7075-T6, aluminium 2024-T4 has a lower tensile strength but can still be used in aerospace industries.
These include aircraft fuselages, transport vehicle sections, and aerofoil stress elements made from aluminium 2024-T4. However, this aluminium grade has low corrosion resistance and is extremely sensitive to thermal shock; therefore, product development teams should be aware of this.
The material's ultimate tensile strength is 20 to 540 MPa, and the elongation percentage before breaking is 14 to 20%. The hardness of the material is measured at 70 to 120 HRB, while the modulus of elasticity is 71 to 73 GPa.
Aluminium MIC 6
Aluminium MIC 6 was created using a novel alloy and casting technique combination to produce sturdy, incredibly high plates. This material is an excellent choice for stress-relieving applications with precision and mechanical properties. Contamination and porosity are absent from Aluminium MIC 6. Industrial components, electronics, and even laser technology all use this silky, lightweight material as an option.
MIC 6 threads have lower tensile strength than those made from 6061, which can contribute to premature yarn rupture with fine-tipped threads. Product designers need to be aware of this limitation while making material choices.
The material's ultimate tensile strength is 166 MPa, and the percentage of elongation before breaking is 3%. The hardness of the material is measured at 65 HRB, while the modulus of elasticity is 71 GPa.
Aluminium 6082
The tensile strength of aluminium 6082 is somewhat higher than that of aluminium 6061. The highest corrosion resilient alloy in the 6000 series, with a maximum strength of any 6000 series alloys. 6082 is a fantastic choice for engineers that need more strength than 6061 but don't want to invest in the 7000 families of materials.
Typical uses for aluminium 6082 include those that require additional strength and hardness. Many bridges, skyscrapers, and other structures in the construction industry use this material. Although aluminium 6082 is tough to work with, product designers should bear this in mind.
The material's ultimate tensile strength is 140 to 340 MPa, and the elongation percentage before breaking is 6.3 to 18%. The hardness of the material is measured at 35 to 56 HRB, while the modulus of elasticity is 69 to 71 GPa.
Employ the Appropriate Material
Aluminium is a robust, malleable, and corrosion-resistant material. For high-performance applications, aluminium alloys 2024-T4, 7075-T6, and 6082 are the best options, while 6061 and MIC 6 can be used in most circumstances.
Choosing the right materials for a given project can be challenging due to CNC machining's wide range of applications. For this reason, organizations may look for alternatives to aluminium for CNC machining. Despite these drawbacks, aluminium is still a viable option for steel because of its high costs and oxidation coating, which can damage tooling.
ALTERNATIVES TO ALUMINUM IN CNC MACHINING
Here are some potential machining alternatives to aluminium, emphasizing their differences and similarities to the popular silver-grey metal.
Metals
Steel & stainless steel
CNC machining frequently employs steel and stainless steel as raw materials. Steels generally are preferred for high-strength applications and those requiring strong welds. Steels can withstand extremely high temperatures, and heat treatment of stainless steels improves their immunity to oxidation.
Even though machining steels are designed to have better machinability, aluminium is still more malleable and ductile than steel. With its increased rigidity to aluminium, steel may be advantageous in some cases but not in others, depending on the application.
Steel may be an appropriate alternative to aluminium if thermal tolerance is a primary concern and mass is not.
Titanium
It is possible to employ titanium as a substitute for aluminium since it has an excellent strength-to-weight ratio—which aluminium has as well. While titanium is lighter than aluminium, its tensile strength is nearly two times greater. Similar to aluminium, it has a good corrosion resilience.
The greater cost of titanium is a reflection of these advantages. Even while this material is a great option for things like airplane components and medical gadgets, the price tag can be prohibitive for certain people.
Titanium is a good substitute for aluminium when lightweight is of the utmost importance and, more crucially, where the manufacturing budget allows for some wiggle room.
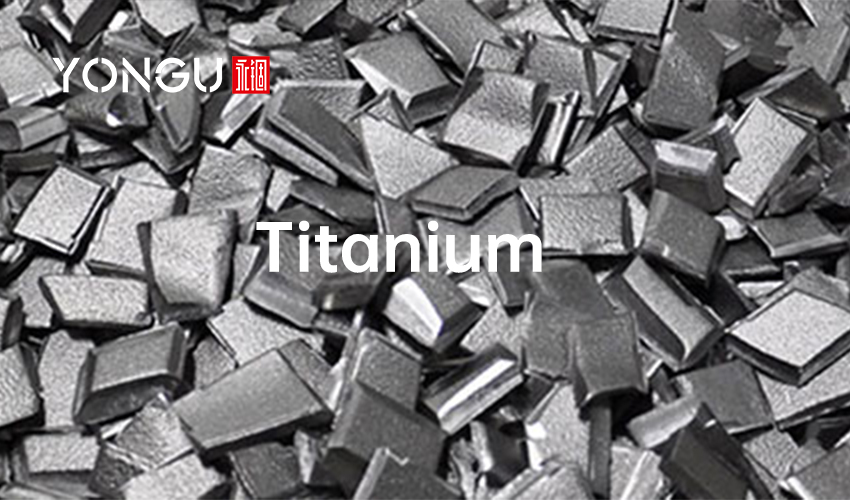
Magnesium
Magnesium, a lightweight metal, has many of the advantages of aluminium alloys, despite its lack of widespread use. Magnesium is a highly machinable metal, allowing for a quick and effective machining process.
For machine shops, there could be a disadvantage. Magnesium chips are exceedingly combustible, and the fact that they are exacerbated by water means that machinists need to exercise extra caution when sweeping away waste.
Brass
Brass is a metal with high aesthetic properties that are highly machinable and can be purchased at a price point that is only somewhat more than that of aluminium. Because of its great machinability and widespread use in structural components like valves and nozzles, this material is well-suited to large-scale production runs.
Copper
Aluminium and copper have a lot of factors in common. Even so, copper's stronger electrical conductivity can make it a better choice for some electrical uses. The machinability of many copper alloys is comparable to that of typical aluminium grades, even though pure copper is difficult to work with.
Thermoplastics
Polyoxymethylene (Delrin)
It's not just metals that can be machined with CNC. On the other hand, aluminium has many advantages that can be matched or even exceeded by engineered thermoplastics, depending on the application.
Delrin is a feasible plastic alternative to aluminium because of its superior machinability, which is why it is widely used. It is a plastic with a low melting point yet a surprising amount of strength.
Insulation makes it useful for parts such as electronic enclosures. It can also be used for mechanical components. Only in cases where thermal and electrical conductivity is of little concern may this material be utilized as a replacement for aluminium, given its dramatically different insulating properties.
Polytetrafluoroethylene (Teflon)
Teflon is a thermoplastic that can be machined easily and is a superb electrical insulator. Conversely, Teflon can withstand temperatures as high as 260°C, making it an appealing high-temperature aluminium substitute.
Teflon's great chemical durability makes it a preferred machining material for food-grade items.
Polyetheretherketone (PEEK)
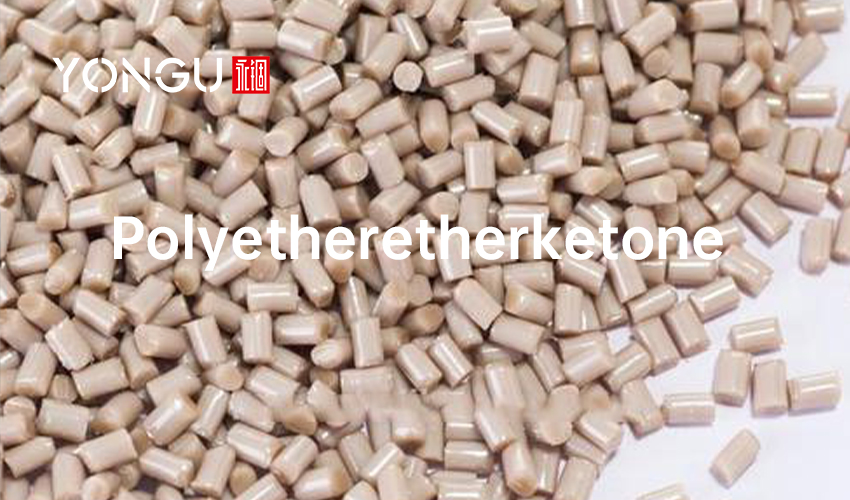
The excellent rigidity and thermal stability of PEEK make it a legitimate resembling replacement for aluminium, even though it is more difficult to machine. The widespread use of PEEK in various common mechanical components is a testament to its metal-like properties.
The cost of the product is a major stumbling hurdle. PEEK is among the most expensive machinable thermoplastics because of its excellent performance, making it only suited for machining tasks where common materials like aluminium are ineffective.
Acrylonitrile Butadiene Styrene (ABS)
In recent years, ABS has been employed as a screen printing filament and as an injection moulding material. On the other hand, ABS has little in common with aluminium but is nevertheless a useful CNC machining material because of its significant potential durability and lightweight.
YONGUBOX's team of skilled designers and engineers can make a material selection for your enclosures easier thanks to their decades of technical experience. We are dedicated to helping every customer innovate and achieve their desired results throughout the production process. Our experienced consulting services give teams peace of mind knowing that their material choice will meet all important standards.
YONGU Aluminium CNC Machining Cases
The YONGU A Series CNC Machine cases contribute while designing the CNC machines as they have their benefits when merged with CNC machines which are to be used in every industry. YONGU provides customers with the ability to customize enclosures in all three dimensions.
YONGU Electronic Industrial Chassis A03 260mm3U
CNC Enclosures made by YONGU provide several advantages in the production process.
- Aluminium CNC Machining Case
- Customizable thickened panels with precision processing
- Strong load-bearing capacity
- Easy Installation
- Heat dissipation is built into the side plates of the enclosure, which improves the function of heat dissipation and lends an air of elegance to the cabinet's essentially pragmatic and industrially designed appearance.
- The front, rear, side handles, and side corners are all CNC processed to give you a technological sensation.
- Inner plates can reduce the fixing problems such as screws and rivets on the surface.
- The length, breadth, and height may all be adjusted. The length may be extended or lowered in increments of 50mm or 100mm as one unit.
- Customizable dimensions, cut out, colours, printing, etc.
- Screws use unique models to enhance your equipment safety.
- The rubber foot pads can be slip-proof and moisture-proof and have a protective effect on internal components.
For further information and customized product of your requirements, please follow our FACEBOOK for more updates and informations.
You can also contact us at +86 13326782625 or write us [email protected].